通過(guò)對(duì)樹(shù)脂聚合過(guò)程的研究,包括樹(shù)脂聚合過(guò)程中溫度、壓力等參數(shù)對(duì)樹(shù)脂聚合的影響等,為纖維增強(qiáng)熱塑性復(fù)合材料原位聚合成型技術(shù)的應(yīng)用奠定了基礎(chǔ)。使用合適的樹(shù)脂與引發(fā)體系,在纖維周圍原位聚合高聚物,從而制備性能優(yōu)異的熱塑性復(fù)合材料。對(duì)PA6(Polyamide 6)樹(shù)脂的陰離子聚合研究起始于19世紀(jì)30年代,這一體系對(duì)于反應(yīng)條件參數(shù)的控制與反應(yīng)潔凈度要求非常高。對(duì)這一問(wèn)題的研究催生了最早的密封混料設(shè)備,進(jìn)一步發(fā)展出結(jié)構(gòu)反應(yīng)注射 SRIM(Structural reaction injection molding )與真空注射VI(Vacuum Infusion) 成型技術(shù)。這些技術(shù)保證了反應(yīng)環(huán)境的清潔度,對(duì)于溫 度壓力的控制非常精細(xì),能夠滿足這一高性能材料的成型要求。同時(shí)將成型周期縮短至數(shù)分鐘,大幅提高了生產(chǎn)效率。對(duì)PMMA(Polymethyl methacrylate )樹(shù)脂原位聚合制備大型結(jié)構(gòu)件的研究主要集中于其熱量傳導(dǎo)方面,制備厚制件與大尺寸制件過(guò)程中傳質(zhì)傳熱問(wèn)題非常突出。研究者設(shè)計(jì)了種類繁多的引發(fā)體系,關(guān)注了其誘導(dǎo)時(shí)間、凝膠時(shí)間點(diǎn)等反應(yīng)動(dòng)力學(xué)過(guò)程。同時(shí),一部分研究者關(guān)注了熱量傳導(dǎo)的模擬,預(yù)測(cè)了制備復(fù)合材料的最大厚 度。這些研究共同推動(dòng)了 PMMA 樹(shù)脂原位聚合成型技術(shù)的發(fā)展,使用這一方法成功制備了大型整體船身結(jié)構(gòu)。另外,學(xué)者們還研究了 PBT( Polybutylene terephthalate)等結(jié)晶性樹(shù)脂在聚合過(guò)程中的結(jié)晶性能變化,為該類樹(shù)脂的成型提供了理論支撐。
本文綜述了纖維增強(qiáng)熱塑性復(fù)合材料原位聚合成型技術(shù)的研究進(jìn)展,詳述了幾種較為常用的成型技術(shù),熱塑性樹(shù)脂傳遞模塑 T?RTM (Thermoplastic resin transfer molding)、結(jié)構(gòu)反應(yīng)注射 SRIM 與真空注射 VI, 分別討論了使用這些技術(shù)的研究實(shí)例,分析了每種技術(shù)的特點(diǎn)與關(guān)鍵點(diǎn)。概述了幾種熱塑性復(fù)合材料原位聚合成型技術(shù)的其他方法。最后,綜合討論了纖維增強(qiáng)熱塑性復(fù)合材料原位聚合成型技術(shù)的共性問(wèn)題,展望了纖維增強(qiáng)熱塑性復(fù)合材料原位聚合技術(shù)的發(fā)展趨勢(shì).
引言
相較于熱固性復(fù)合材料,纖維增強(qiáng)熱塑性復(fù)合材料具有韌性高、成型周期短、制備效率高、可回收和二次加工的優(yōu)點(diǎn),這使其不僅滿足了軍用領(lǐng)域?qū)Ω邠p傷容限性能的需求,還滿足了民用領(lǐng)域?qū)档统杀?、提高生產(chǎn)率的需求,這些年逐漸成為科研領(lǐng)域的研究熱點(diǎn)。纖維增強(qiáng)熱塑性復(fù)合材料的制備方法從原理上可分為兩大類:一類是發(fā)展較早的熱熔方法 ,一類是原位聚合方法。
熱熔法一般需要高溫高壓來(lái)驅(qū)動(dòng)長(zhǎng)鏈高分子樹(shù)脂流動(dòng)浸漬纖維,由于樹(shù)脂粘度較大,微觀尺度樹(shù)脂很難完全浸漬纖維,導(dǎo)致產(chǎn)品局部孔隙含量較高,留下較多的缺陷。
原位聚合方法使用低粘度單體或寡聚物前體浸漬纖維,有以下幾點(diǎn)優(yōu)勢(shì):(1)由于樹(shù)脂粘度低,不需要高溫高壓條件即可獲得比目前可達(dá)到的熔體處理工藝更大、更厚、更集成的產(chǎn)品,如圖1所示;(2)可以獲得樹(shù)脂對(duì)纖維浸漬優(yōu)良的制件 (制件質(zhì)量更均一、力學(xué)性能更優(yōu));(3)由于樹(shù)脂聚合發(fā)生在纖維表面,故纖維與樹(shù)脂間能夠形成較強(qiáng)的化學(xué)鍵連接;(4)可以在織物增強(qiáng)的基礎(chǔ)上,添加納米粒子到未反應(yīng)的單體中,獲得分布均勻的纖維增強(qiáng)聚合物納米復(fù)合材料;(5) 工藝周期更短,生產(chǎn)效率高。
圖1 兩種工藝制備的各類樹(shù)脂粘度分布
纖維增強(qiáng)熱塑性復(fù)合材料原位聚合的成型方法大多來(lái)源于熱固性復(fù)合材料已經(jīng)發(fā)展完善的成型方法,一些成型方法與原有方法基本一致,另一些方法在原有基礎(chǔ)上針對(duì)熱塑性樹(shù)脂的特點(diǎn)進(jìn)行了較大改動(dòng),這些不同源自于熱塑性樹(shù)脂與熱固性樹(shù)脂特性之間的顯著差異。熱塑性樹(shù)脂和熱固性樹(shù)脂聚合速率均隨溫度的升高而增加,然而,一些熱塑性樹(shù)脂具有半晶性質(zhì),結(jié)晶受到溫度的影響 。當(dāng)溫度過(guò)低時(shí),結(jié)晶速度過(guò)快,反應(yīng)鏈末端和單體在聚合之前就被困在晶體內(nèi);當(dāng)溫度過(guò)高時(shí),結(jié)晶度降低,導(dǎo)致聚合物強(qiáng)度、剛度和耐化學(xué)性變差。另外,一些反應(yīng)性熱塑性材料,如 PMMA(聚甲基丙烯酸甲酯)、PA6(聚酰胺 6)、PA12(聚酰胺 12) 和 PBT(聚對(duì)苯二甲酸丁二醇酯),其熔體粘度比普通熱固性樹(shù)脂低一個(gè)數(shù)量級(jí)。因此,纖維預(yù)成型體在浸漬過(guò)程中產(chǎn)生的毛細(xì)力較大,充模過(guò)程中可能形成孔洞和流道。
最早用于制備復(fù)合材料的原位聚合法是鑄造成型,這種方法工藝簡(jiǎn)單且成本低,適用于制造大型產(chǎn)品 。由于技術(shù)的快速發(fā)展,該方法已難以適應(yīng)目前使用連續(xù)纖維或者織物作為增強(qiáng)體的現(xiàn)狀。本文綜述了纖維織物增強(qiáng)的熱塑性復(fù)合材料原位聚合成型方法,包括熱塑性樹(shù)脂傳遞模塑(T?RTM)、結(jié)構(gòu)反應(yīng)注射(SRIM)、真空注射(VI)、樹(shù)脂膜熔滲(PFI)等。針對(duì)每種成型方法, 本文綜述了主要的應(yīng)用實(shí)例以及相關(guān)研究前沿進(jìn)展,評(píng)價(jià)了每種方法的特點(diǎn)。
合成型技術(shù)
本章著重從織物增強(qiáng)熱塑性原位聚合成型技術(shù)方面展開(kāi),詳述了幾種原位聚合成型技術(shù)。從技術(shù)發(fā)展概況、使用實(shí)例以及技術(shù)特征等角度討論了熱塑性原位聚合成型技術(shù), 并進(jìn)一步對(duì)使用其他形式增強(qiáng)體的工藝進(jìn)行了討論,以供對(duì)比分析。
1. 樹(shù)脂傳遞模塑 T?RTM
在生產(chǎn)纖維增強(qiáng)熱塑性復(fù)合材料時(shí),主要考慮的是基體樹(shù)脂的粘度。如果能充分降低熱塑性塑料的粘度,熱塑性樹(shù)脂轉(zhuǎn)移模塑(T?RTM)等熱固性樹(shù)脂生產(chǎn)技術(shù)可用于熱塑性復(fù)合材料的加工,如圖 2 所示。Mairtin 等提出了使用液體浸漬方法時(shí),樹(shù)脂需要滿足的三點(diǎn)要求:(1)樹(shù)脂粘度低于 1Pa·s ;(2)完成浸漬后,樹(shù)脂能夠在短時(shí)間內(nèi)發(fā)生化學(xué)或物理變化,達(dá)到硬化;(3)最終樹(shù)脂性能滿足制件需求。Luisier等在其基礎(chǔ)上增加了第四條要求,即反應(yīng)無(wú)副產(chǎn)物生成。
圖2 T?RTM 成型工藝
Parton等遵循這四條要求,選擇Cyclics公司的 CBT 前驅(qū)體作為基體樹(shù)脂(錫基催化劑),選擇兩種玻纖織物作為增強(qiáng)相,使用真空輔助T?RTM 工藝制備復(fù)合材料平板(尺寸為 320mm×200mm×2mm)。設(shè)定真空度從0.14 MPa到 0.08 MPa,控制充模時(shí)間,如圖3所示??剂苛藰?shù)脂組分?jǐn)嚢钑r(shí)間、充模時(shí)間對(duì)復(fù)合材料板材制備質(zhì)量的影響。研究發(fā)現(xiàn),對(duì)于這種工藝窗口很短的樹(shù)脂體系,較長(zhǎng)(從 12 s 延長(zhǎng)至 30 s)的攪拌時(shí)間會(huì)導(dǎo)致復(fù)合材料浸漬不充分。進(jìn)一步對(duì)浸漬充分的試樣進(jìn)行了彎曲性能測(cè)試分析,發(fā)現(xiàn)單向玻纖復(fù)合材料的彎曲強(qiáng)度為 775 MPa,略低于理論預(yù)測(cè)值 850 MPa,原因是制件中有一些區(qū)域的孔隙率達(dá)到 4.2%。Parton 等的研究開(kāi)拓了熱塑性復(fù)合材料的液體成型方法,且他們得出了一些重要的結(jié)論,如對(duì)于工藝窗口較小的樹(shù)脂體系,工藝參數(shù)的控制極為重要,需要精確設(shè)定。
圖3 T?RTM 工藝流程
Achilias 等推導(dǎo)了擴(kuò)散控制的反應(yīng)速率模擬計(jì)算公式,詳細(xì)論述了自由基聚合過(guò)程中的動(dòng)力學(xué)機(jī)理。2015 年, Alexander Zoller 等最早開(kāi)始研究 BPO(過(guò)氧化苯甲酰)/ DMA(二甲基苯胺) 室溫引發(fā) MMA(甲基丙烯酸甲酯) 樹(shù)脂的聚合動(dòng)力學(xué)模擬。2017 年,美國(guó)科羅拉多大學(xué)的 Suzuki 等以 MMA 樹(shù)脂為基體、玻纖為增強(qiáng)體,研究了樹(shù)脂聚合的動(dòng)力學(xué) ,并引入了一維熱傳導(dǎo)方程建立板材傳熱模型, 模擬計(jì)算了不同厚度板材的溫度歷程。同時(shí), 他們還使用室溫引發(fā)的氧化還原體系,以 BPO 為氧化劑、 DMT(二甲基對(duì)甲苯胺)為還原劑,采用 T?RTM 工藝制備了復(fù)合材料,并用紅外攝像機(jī)對(duì)板材成型過(guò)程中的溫度進(jìn)行了測(cè)量。結(jié)果表明:引發(fā)劑濃度提高使凝膠效應(yīng)提前,峰值溫度變高,與模型預(yù)測(cè)值較為吻合,如圖 4 所示。他們實(shí)驗(yàn)測(cè)量了傳熱系數(shù), 將現(xiàn)有的 MMA 聚合模型與一維傳熱模型聯(lián)立,同時(shí)考慮了效率因子,模擬了樹(shù)脂反應(yīng)的溫度變化歷程,合理捕獲了初 始濃度改變時(shí)的誘導(dǎo)時(shí)間和最大溫度。他們進(jìn)一步運(yùn)用這 一模型預(yù)測(cè)了板材的最大厚度(在他們的實(shí)驗(yàn)條件下是40cm)。Suzuki 等同時(shí)驗(yàn)證了預(yù)溶解 PMMA 的量對(duì)聚合動(dòng)力學(xué)的影響。實(shí)驗(yàn)發(fā)現(xiàn),隨著預(yù)溶解 PMMA 的量增多,凝膠效應(yīng)逐步提前。
圖 4 不同引發(fā)劑濃度的模型預(yù)測(cè)(實(shí)線) 與實(shí)驗(yàn)結(jié)果(虛線)對(duì)比
Charlier 等分析了用于復(fù)合材料液體成型(LCM)的丙烯酸反應(yīng)性混合物特性,以制備用于復(fù)合材料的熱塑性基體,并研究了自由基聚合過(guò)程中的轉(zhuǎn)化率、復(fù)粘度和固化放熱性能。結(jié)果表明,這一體系存在凝膠效應(yīng),聚合具有較高的放熱性。流變學(xué)研究表明,LCM 工藝的可注射單體轉(zhuǎn)化率為 10%左右。Charlier 等還建立了甲基丙烯酸甲酯/ 聚甲基丙烯酸甲酯混合物的玻璃化曲線,以確定單體完全轉(zhuǎn)換所需的熱條件,從而調(diào)控殘余單體含量。使用這種基于丙烯酸的反應(yīng)溶液進(jìn)行快速 LCM 成型是可行的,因?yàn)樵?90℃下,反應(yīng) 5min 內(nèi)可以得到完全聚合的樹(shù)脂基體。
Boumbimba等研究了丙烯酸原位聚合制備玻纖織物增強(qiáng)復(fù)合材料的低速?zèng)_擊性能,以及少量丙烯酸嵌段共聚物的添加對(duì)該樹(shù)脂混合物原位聚合的影響,并進(jìn)一步分別在 20 ℃ 、80 ℃和 -80 ℃下分析了嵌段共聚物添加量對(duì)復(fù)合材料低速?zèng)_擊性能的影響。結(jié)果表明,在 20 ℃ 和 80 ℃ 時(shí),共聚物的添加能夠提高復(fù)合材料的沖擊破壞閾值,尤其是 80 ℃ 條件下,最高提高了 24%。但在 -80 ℃ 條件下,共聚物的加入反而使復(fù)合材料的沖擊吸收能有所降低。
美國(guó)伯明翰大學(xué)的 Barfknecht 等在 2016 年提出了一 種新的原位聚合制備 APA-6 復(fù)合材料的思路,通過(guò)將引發(fā)官能團(tuán)沉積到增強(qiáng)纖維上,之后僅注入單體組分進(jìn)行原位聚合。該技術(shù)所需加工設(shè)備簡(jiǎn)單,污染風(fēng)險(xiǎn)較低,極大提高了復(fù)合材料原位聚合的自動(dòng)化程度。用硅烷衍生引發(fā)劑(N-[5-(Trimethoxysilyl)-2-aza-1-oxopentyl]caprolactam )對(duì)玻璃纖維表面引發(fā)聚合進(jìn)行了研究,發(fā)現(xiàn)這一聚合方法能夠在纖維表面形成 PA 原位聚合的引發(fā)點(diǎn),但是制備的板材中心部位樹(shù)脂單體未完全轉(zhuǎn)化。
最近,Louisy 等使用丙交酯樹(shù)脂作為基體,玻纖織物作為增強(qiáng)體,通過(guò) T?RTM 工藝制備了 120 mm× 120 mm×5 mm 的復(fù)合材料板材。分別在實(shí)驗(yàn)室條件和生產(chǎn)條件下研究了催化劑添加量、溫度對(duì)純樹(shù)脂聚合的反應(yīng)時(shí)間、轉(zhuǎn)化率、分子 量、分子量分布的影響。研究發(fā)現(xiàn),在實(shí)驗(yàn)室氬氣保護(hù)環(huán)境中,反應(yīng)時(shí)間為 12 min,聚合度達(dá)到 91%~ 97%;而在空氣環(huán)境中,反應(yīng)時(shí)間延長(zhǎng)至 40 min,樹(shù)脂的摩爾質(zhì)量下降了一半以上,說(shuō)明大氣環(huán)境對(duì)這一樹(shù)脂體系的聚合產(chǎn)生了較大的影 響。Louisy 等進(jìn)一步研究了添加玻璃纖維使用 T?RTM 制備復(fù)合材料對(duì)樹(shù)脂聚合的影響,發(fā)現(xiàn)玻纖對(duì)樹(shù)脂聚合程度的影響很小,樹(shù)脂仍能在足夠的反應(yīng)時(shí)間下達(dá)到較高的轉(zhuǎn)化率。不同的是,模具中的樹(shù)脂聚合反應(yīng)無(wú)法攪拌(實(shí)驗(yàn)室中反應(yīng)伴隨攪拌),因此聚合時(shí)間延長(zhǎng)至 2~3 h,聚合物分子量也有所降低。
綜上,熱塑性復(fù)合材料的 T?RTM 工藝作為熱塑性復(fù)合材料原位聚合的首要方法,能夠制備質(zhì)量較好的復(fù)合材料。同時(shí),該方法較成熟、效率高且成本低。然而,與熱固性 RTM工藝相比,仍需要注意以下幾點(diǎn):
(1) T?RTM 工藝需要對(duì)反應(yīng)參數(shù)進(jìn)行更加精確的控制,這基于對(duì)樹(shù)脂反應(yīng)動(dòng)力學(xué)的研究更加全面和深入。
(2)對(duì)于一些反應(yīng)熱較大的樹(shù)脂體系,僅從工藝或反應(yīng)物濃度單方面進(jìn)行研究已經(jīng)不能滿足工業(yè)需求,需要從新的引發(fā)體系、反應(yīng)物濃度、反應(yīng)動(dòng)力學(xué)、工藝參數(shù)控制和傳熱模 擬共同考量,綜合研究出適合的原位聚合方法。
(3)一些生產(chǎn)中的實(shí)際環(huán)境因素與實(shí)驗(yàn)室有所區(qū)別,對(duì)樹(shù)脂聚合有不小的影響。
1. 結(jié)構(gòu)反應(yīng)注射 SRIM
結(jié)構(gòu)反應(yīng)注射工藝與熱固性復(fù)合材料的 RTM 工藝密切相關(guān),如圖 5 所示。該工藝與 RTM 工藝相同的部分是纖維增強(qiáng)體均放置在兩個(gè)硬模具之間,后期樹(shù)脂注入浸漬纖維進(jìn)行聚合。不同的是,這個(gè)工藝為了防止樹(shù)脂過(guò)早的聚合,增加了反應(yīng)物料輸入系統(tǒng),反應(yīng)性樹(shù)脂組分被分離,在進(jìn)入模具前進(jìn)行定量混合,使用高壓(0.8~1 MPa)浸漬干纖維。
圖5 結(jié)構(gòu)反應(yīng)注射工藝原理圖
結(jié)構(gòu)反應(yīng)注射成型方法最早是 Karger-Kocsis 等于 1992 年提出的。他們使用玻纖織物增強(qiáng)尼龍嵌段共聚物原位聚合制備了復(fù)合材料,采用光鏡和聲發(fā)射(AE)同時(shí)監(jiān)測(cè)的方法研究了玻璃纖維(GF)束氈增強(qiáng)尼龍嵌段共聚物(NBC)的破壞模式。結(jié)果發(fā)現(xiàn):在裂紋萌生階段(最大載荷階段)和裂紋擴(kuò)展階段,其破壞模式存在較大的差異。前一階段裂紋尖端鈍化,后一階段纖維氈網(wǎng)狀變形,并伴有相應(yīng) 的脫粘、纖顫和組成纖維及其細(xì)絲的斷裂。當(dāng)超過(guò)最大載荷時(shí),基體的變形模式由韌性屈服轉(zhuǎn)變?yōu)檎承运毫选?/span>
2013 年,PPG 公司從商業(yè)角度報(bào)道了使用 SRIM 工藝制備 APA-6 玻纖復(fù)合材料的優(yōu)勢(shì):由于實(shí)現(xiàn)了實(shí)時(shí)混合物料,可以極大地縮短樹(shù)脂混合與充模時(shí)間,工藝周期縮短至 3min,每天可生產(chǎn) 500 件產(chǎn)品;相比于金屬構(gòu)件減少了 50%的質(zhì)量;制備的復(fù)合材料內(nèi)部質(zhì)量?jī)?yōu)良、無(wú)空隙,玻纖含量可達(dá) 70%,力學(xué)性能與環(huán)氧相當(dāng),可以用于結(jié)構(gòu)件。
德國(guó)恩格爾奧地利有限公司研究了 SRIM 工藝制備復(fù)合材料車身結(jié)構(gòu)的性能,發(fā)現(xiàn) APA-6 之所以能夠被廣泛用于熱塑性液體成型工藝的原因是:這一樹(shù)脂在室溫時(shí)為結(jié)晶固體,在達(dá)到熔點(diǎn) 70℃ 后能夠非常迅速地轉(zhuǎn)變?yōu)檎扯燃s 10 MPa·s 的液體。這一特性使得 APA-6 能夠充分浸漬增強(qiáng)體纖維,使得制備的復(fù)合材料內(nèi)部質(zhì)量?jī)?yōu)良。
結(jié)構(gòu)反應(yīng)注射充模工藝具有如下優(yōu)點(diǎn):
(1)工藝周期非常短,通常在工業(yè)生產(chǎn)中僅為3~5 min;
(2)反應(yīng)條件潔凈;
(3)工藝參數(shù)控制精確,反應(yīng)物預(yù)熱,計(jì)量混合均為機(jī)械控制。
但是,此工藝缺點(diǎn)也很明顯,如設(shè)備成本高,實(shí)驗(yàn)室研究難以承受等。
3. 真空注射 VI
真空注射工藝與 VARI 工藝類似,充模速度較低,大氣壓力足以使模具夾緊,因此最大可實(shí)現(xiàn)部件尺寸僅受反應(yīng)體系的時(shí)間限制。在混合了兩罐中的原料后,反應(yīng)性混合物被注入到一個(gè)緩沖容器中,用來(lái)分離注入所需的壓力和促進(jìn)輸液所必需的真空,如圖 6 所示。
荷蘭代爾夫特理工大學(xué)的 Rijswijk 團(tuán)隊(duì)最早開(kāi)始進(jìn)行真空注射成型工藝的研究。他們?cè)谥苽滹L(fēng)電葉片的項(xiàng)目(2005年)中, 研究使用了新的樹(shù)脂體系 APA-6 來(lái)替代環(huán)氧,以期降低制造成本。這一想法基于這一團(tuán)隊(duì)前期對(duì) APA-6 陰離子聚合過(guò)程的熟知(他們?cè)?003 年對(duì) APA-6 的引發(fā)體 系進(jìn)行了研究),對(duì)于不同配比的引發(fā)劑組分與形成的聚合物性能有了較為詳細(xì)的數(shù)據(jù)儲(chǔ)備。由于 APA-6 的陰離子聚合對(duì)實(shí)驗(yàn)條件的潔凈度要求很高,他們自制了一個(gè)簡(jiǎn)易的混料設(shè)備,如圖7所示。Rijswijk 首先研究了引發(fā)劑和催化劑添加量對(duì)樹(shù)脂聚合反應(yīng)的影響,隨后研究了 APA-6 的工藝溫 度與壓力的可調(diào)范圍,獲得了合適的工藝流程,分別制備了 玻纖和碳纖增強(qiáng)的 APA-6 原位聚合復(fù)合材料,其綜合力學(xué)性能略低于環(huán)氧復(fù)合材料。
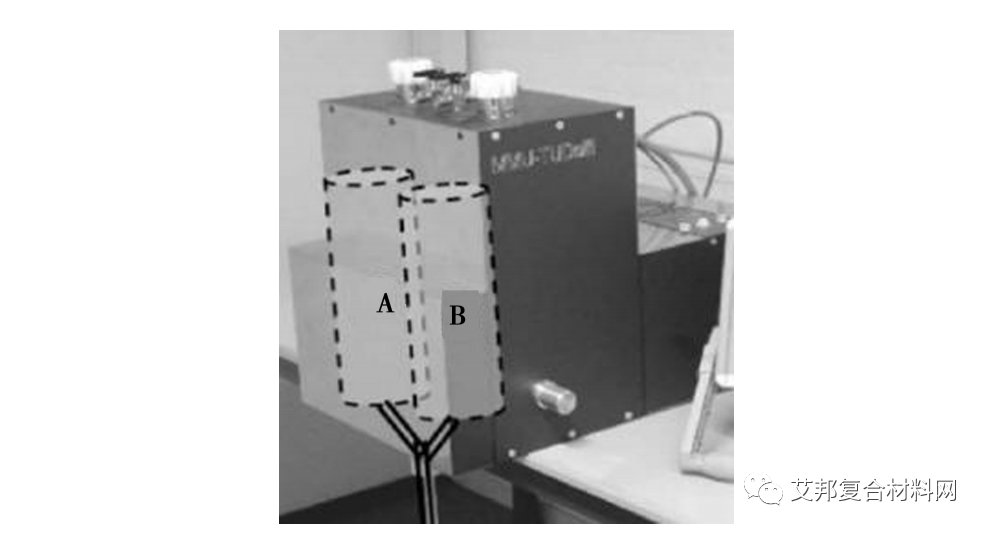
圖7 微型混料單元
Rijswijk 等進(jìn)一步研究了聚合溫度對(duì)真空注射制備 APA-6 板材質(zhì)量的影響。結(jié)果表明,聚合溫度的提高對(duì)單體轉(zhuǎn)化率影響較小,但是隨聚合溫度從 140℃ 升高到 170℃ ,分子量從 42000 提高到了 90000,密度與孔隙率也有小幅提升。這些影響綜合反映在樹(shù)脂板材的力學(xué)性能上,其中在 150 ℃聚合溫度下得到的材料強(qiáng)度和模量最高,這可能與 PA 的結(jié)晶性能有關(guān)。
中科院寧波所的顏春等在 Rijswijk 團(tuán)隊(duì)研究基礎(chǔ)上, 探討了APA-6 原位聚合方法的引發(fā)體系添加量以及復(fù)合材料的力學(xué)性能,重點(diǎn)從結(jié)晶的角度對(duì)其力學(xué)性能進(jìn)行了分析。研究結(jié)果表明,隨著聚合溫度從 140℃ 升高到 180℃ ,連 續(xù) GF/APA-6 復(fù)合材料基體樹(shù)脂的結(jié)晶度從 52.7%逐漸降低至 36.1%。當(dāng)聚合溫度為 150 ℃ 、聚合時(shí)間為 45 min 時(shí),其 力學(xué)性能達(dá)到最高,拉伸強(qiáng)度為538.1 MPa,彎曲強(qiáng)度為 497.2 MPa,層間剪切強(qiáng)度為 52.5 MPa。中科院寧波所還對(duì) CBT 開(kāi)環(huán)聚合致脆的機(jī)理進(jìn)行了研究,發(fā)現(xiàn) CBT 的開(kāi)環(huán)聚合 致脆原因主要是樹(shù)脂前體純度問(wèn)題,在熔化聚合時(shí),由于單體熔化溫度不同,導(dǎo)致一部分熔點(diǎn)高的單體被包裹在已反應(yīng)的長(zhǎng)鏈分子中,形成鉚釘作用。對(duì)此,他們對(duì)樹(shù)脂前體進(jìn)行提純,使所有樹(shù)脂前體同時(shí)熔化和聚合,解決了這一問(wèn)題。
西班牙的Agirregomezkorta等近幾年研究了真空注射工藝參數(shù)對(duì) CBT 復(fù)合材料沖擊性能的影響。使用了碳纖維作為增強(qiáng)體,制備了 250 mm×250 mm×3.6 mm 的板材,主要研究了兩種非等溫工藝條件對(duì)材料性能的影響,其中一種是短周期快速冷卻(熔點(diǎn)以上保持 5 min,33℃/ min 降溫速率),另一種是長(zhǎng)周期慢冷卻(熔點(diǎn)以上保持 1h,3.5℃/ min 降溫速率)。一方面,在結(jié)晶收縮過(guò)程中,快速冷卻會(huì)在富樹(shù)脂區(qū)域產(chǎn)生隨機(jī)分散的孔隙。另一方面,緩慢冷卻材料的內(nèi)部沒(méi)有孔隙,但結(jié)晶度較高,因此材料較脆。由于基體的脆性和縱向收縮的共同作用,富樹(shù)脂區(qū)出現(xiàn)了許多微裂紋。慢冷復(fù)合材料的臨界分層能略高于快冷復(fù)合材料的臨界分層能,而快冷復(fù)合材料在滲透前吸收的能量比慢冷復(fù)合材料高 25%以上,表現(xiàn)出較低的脆性。
VI 工藝的優(yōu)點(diǎn)主要有以下幾點(diǎn):(1)生產(chǎn)的部件大小幾乎不受限制;(2)加入了物料混合系統(tǒng),能夠制備對(duì)反應(yīng)條件非常敏感的樹(shù)脂;(3)需要的壓力較低,一般為一個(gè)大氣壓或更低;(4)成本低;缺點(diǎn)是模具通常只能使用一次,并且產(chǎn)品一側(cè)的表面質(zhì)量較差。
4. 其他工藝
本節(jié)包括一些研究較早、目前應(yīng)用較少或方法特殊的熱塑性復(fù)合材料制備工藝,包括但不限于纖維織物作為增強(qiáng)體。
4.1 樹(shù)脂膜熔滲
樹(shù)脂膜熔滲(Resin film infusion ,RFI)類似于熱固性復(fù)合材料的預(yù)加工:在模具中交替堆疊纖維層和未反應(yīng)的活性樹(shù)脂混合物層。施加熱量和壓力時(shí),薄片熔化并浸漬纖維, 之后聚合開(kāi)始,如圖 8 所示。由于薄膜沒(méi)有足夠的力學(xué)性能,需將其直接鋪覆在支撐纖維織物上,同時(shí)也可以使用粉末浸漬的織物。在熔化和浸漬過(guò)程中,鋪層體積大幅減少, 通常需要多個(gè)壓實(shí)步驟來(lái)壓縮鋪層。在這種情況下,反應(yīng)性混合物的粘度同樣需要低于1Pa·s。較厚的部分壓實(shí)困難,通常需要兩面剛性模具,加上較大的壓力,同時(shí)使用低粘度的低聚物前體。
圖8 樹(shù)脂膜熔滲工藝
RFI 的主要優(yōu)點(diǎn)是安裝簡(jiǎn)易和快速浸漬,而缺點(diǎn)是增加了壓實(shí)過(guò)程。
4.2 反應(yīng)注射拉擠
熱塑性反應(yīng)注射拉擠工藝(Thermoplastic reaction injection pultrusion)是最近才成為人們感興趣的制備方法,如圖9 所示。這一工藝的材料和設(shè)備開(kāi)發(fā)最新進(jìn)展及其巨大的商業(yè)潛力,激發(fā)了人們的興趣 。該工藝是使用連續(xù)纖維作為增強(qiáng)體,將反應(yīng)性的熱塑性樹(shù)脂實(shí)時(shí)混合加入模腔中,邊浸漬纖維邊聚合。在模具的后端進(jìn)行冷卻,直接連續(xù)成型所需形狀的型材。
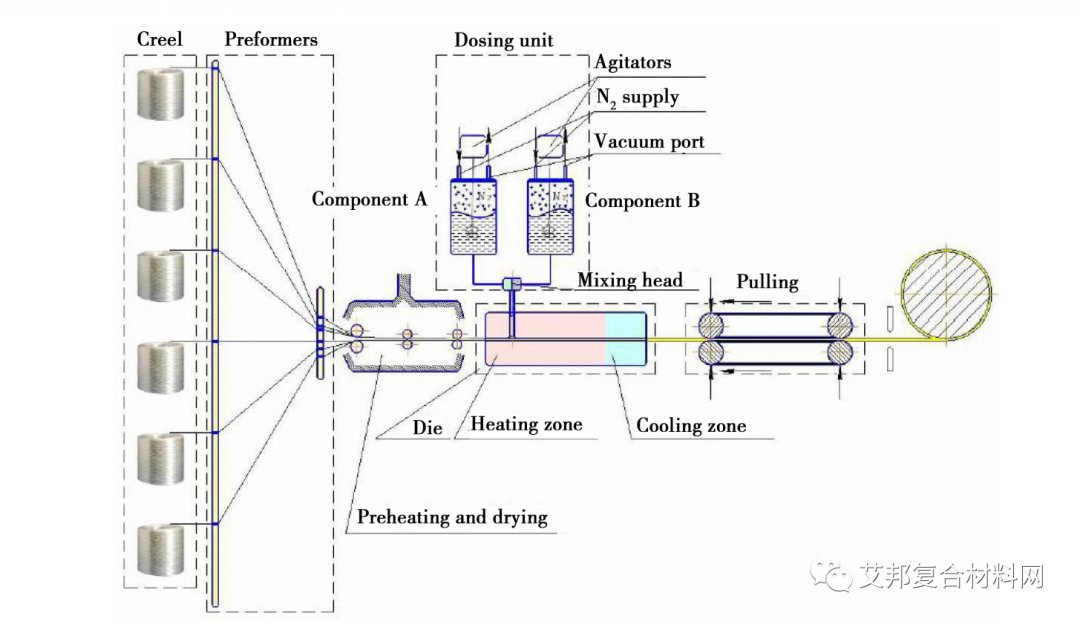
圖9 反應(yīng)注射拉擠
德國(guó)斯圖加特大學(xué)的 Epple 等研究了反應(yīng)注射拉擠成型玻纖增強(qiáng) PA-6 復(fù)合材料的成型性能。他們選擇活化劑濃 度為 2.5%,催化劑濃度為 3.75%,制備了復(fù)合材料型材,如圖10 所示。結(jié)果表明,采用反應(yīng)注射拉擠法可生產(chǎn)出連續(xù)的玻璃纖維增強(qiáng) PA-6 零件。為了評(píng)價(jià)反應(yīng)注射拉擠工藝生產(chǎn)的零件質(zhì)量,必須在進(jìn)一步的試驗(yàn)中分析成型過(guò)程參數(shù)的影響。
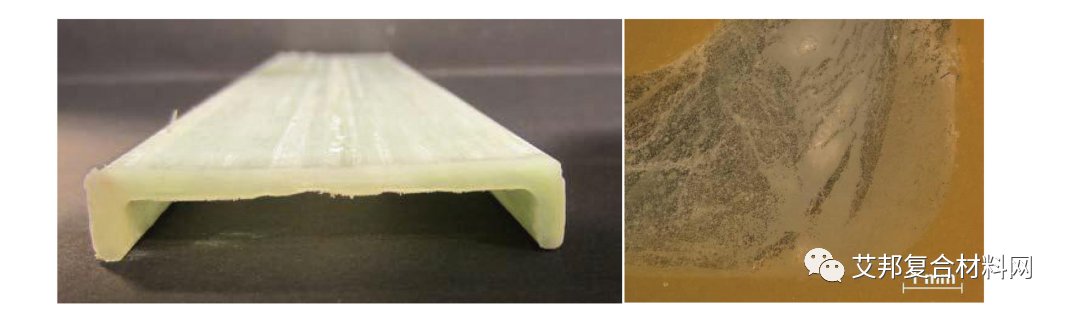
圖10 反應(yīng)注射拉擠制備的玻纖增強(qiáng) PA-6 復(fù)合材料
KraussMaffei 等公司合作開(kāi)發(fā)了一種名為 iPul 的拉擠系統(tǒng),生產(chǎn)速度達(dá)到 3m/min(熱固性材料的速度通常是0.5~1.5 m/min )。CQFD 復(fù)合材料公司等合作為現(xiàn)代汽車開(kāi)發(fā)了拉擠前碰撞梁, 此前碰撞梁使用了單向玻纖增強(qiáng)的陰離子聚合 PA-6 基 體 。這些成功的開(kāi)發(fā)項(xiàng)目證明了其工業(yè)應(yīng)用的可行性。然而,該工藝的流程開(kāi)發(fā)和參數(shù)優(yōu)化是關(guān)鍵問(wèn)題,需要進(jìn)行全面研究,目前其還未得到商業(yè)化應(yīng)用。
反應(yīng)注射拉擠優(yōu)點(diǎn)是可以連續(xù)生產(chǎn)無(wú)限長(zhǎng)度的復(fù)合材料產(chǎn)品,生產(chǎn)效率高,同時(shí)具有熱塑性材料的優(yōu)越性能。缺點(diǎn)是設(shè)備成本較高,制備的制件必須具有相同的截面。
4.3 增材制造 AM
增材制造(Additive Manufacturing ,AM) 在 2010 年就有報(bào)道提及,使用了內(nèi)酰胺的陰離子聚 合。Khodabakhshi等采用傳統(tǒng)的引發(fā)劑(NaCL, CLMgBr=) 和活化劑(n?乙 酰己內(nèi)酰胺),通過(guò)差示掃描量熱法(DSC)測(cè)試,確定噴墨的 最佳配方和條件。使用 AM 法的樹(shù)脂體系凝固半衰期可縮短至1 min以內(nèi)。他們還比較了噴墨 PA-6 與鑄型 PA-6 的性 能,發(fā)現(xiàn)噴墨 PA-6 的轉(zhuǎn)化率、分子量和結(jié)晶度分別為 95%~ 96 %、41~50 kDa 和 38%~40 %,而鑄型 PA-6 的轉(zhuǎn)化率、分子 量和結(jié)晶度分別為 94%、45~52 kDa 和 43% ~44%。
增材制造的優(yōu)點(diǎn)是能夠制造任意形狀的制件,且得到的制件內(nèi)部質(zhì)量均一,內(nèi)應(yīng)力小。缺點(diǎn)是原料成本高。
02
結(jié)語(yǔ)與展望
綜合以上各類纖維增強(qiáng)熱塑性復(fù)合材料原位聚合成型方法的特點(diǎn),可以得出一些區(qū)別于熱固性復(fù)合材料共性的點(diǎn):
(1)部分熱塑性樹(shù)脂粘度較熱固性樹(shù)脂低一個(gè)數(shù)量級(jí), 在充模過(guò)程中需要重視毛細(xì)作用,以免產(chǎn)生流動(dòng)不均導(dǎo)致的缺陷。這一問(wèn)題需要對(duì)樹(shù)脂流變,聚合動(dòng)力學(xué)進(jìn)行更深入的研究,探究合適的樹(shù)脂體系配比,以及更精細(xì)的工藝參數(shù)。
(2)熱塑性樹(shù)脂的制造追求更短的制造周期,以期提高效率降低成本,這對(duì)一些放熱量較大的樹(shù)脂體系提出了不小的挑戰(zhàn),因此工藝中的熱量控制成為一個(gè)重點(diǎn)。這一問(wèn)題的解決有賴于對(duì)樹(shù)脂聚合動(dòng)力學(xué)和傳熱過(guò)程的綜合考量,以及設(shè)備的改進(jìn)。
(3)很大一部分熱塑性樹(shù)脂具有半結(jié)晶性,加工這類樹(shù)脂需要注意結(jié)晶與工藝溫度之間的關(guān)系。因此,工藝后端的降溫過(guò)程對(duì)這些樹(shù)脂來(lái)說(shuō)異常重要。
(4)界面是復(fù)合材料制造和研究中非常重要的部分,成型過(guò)程中對(duì)這一問(wèn)題考慮較少,對(duì)界面的研究大多集中在實(shí)驗(yàn)室。熱塑性復(fù)合材料的上漿劑研究起步較晚,尚無(wú)大范圍應(yīng)用的產(chǎn)品,這一問(wèn)題的解決依賴于熱塑性復(fù)合材料產(chǎn)業(yè)的發(fā)展。
原位聚合熱塑性復(fù)合材料方法由于成本低且綠色環(huán)保, 逐漸成為工業(yè)界關(guān)注的熱點(diǎn)。20 世紀(jì)初,荷蘭發(fā)展的風(fēng)電項(xiàng)目要求制備 3000個(gè)兆瓦級(jí)的風(fēng)力發(fā)電樁,由此引發(fā)了 APA-6 原位聚合方法的大規(guī)模研究,開(kāi)創(chuàng)了這一領(lǐng)域的研究潮流。國(guó)際對(duì)于汽車工業(yè)發(fā)展復(fù)合材料部件的減輕質(zhì)量、降低能耗的需求催生了 PBT 樹(shù)脂原位聚合方法的研究熱潮。同樣,海洋設(shè)備與船舶的發(fā)展需求大尺寸構(gòu)件的制備技術(shù),也會(huì)推動(dòng)熱塑性原位聚合方法的研究。而航空工業(yè)對(duì)高韌性材料的需求也成為研究這一方法的堅(jiān)實(shí)基礎(chǔ)。
對(duì)于纖維增強(qiáng)熱塑性復(fù)合材料的原位聚合成型方法的研究,已經(jīng)呈現(xiàn)出井噴的態(tài)勢(shì)。一方面,對(duì)于既有的樹(shù)脂類型更加深入地研究其聚合過(guò)程,以及新型的引發(fā)體系和聚合方法;對(duì)于更多高性能樹(shù)脂,研究摸索其可以制備的基本方法。另一方面,對(duì)于已有的工藝方法進(jìn)行不斷完善和改進(jìn);對(duì)于新的成型技術(shù)進(jìn)行開(kāi)發(fā),例如反應(yīng)注射拉擠、增材制造與熱塑性復(fù)合材料焊接與修復(fù)技術(shù)。